引言
催化裂化作为炼油、炼化行业的核心加工装置,显然提高装置的生产水平对企业的经济效益起着重要作用。但催化裂化工艺由于其过程的复杂性,很难用精确的反应动力学模型来描述,同时,现场一般也难于提供可靠的质量分析仪表进行检测、分析进料组成的变化。基于这些复杂的情况,采用DCS的常规PID控制很难及时地进行调整,经常造成操作波动,影响装置的经济效益。于是在催化裂化装置应用先进控制(APC)技术就成了众多企业提高效益的明智选择。洛阳石化分公司面对不断变化的市场需求和运行环境,为了取得更好的经济效益,I套催化裂化装置于2012年5月引入先进控制系统。此系统投用以来已连续运行两年多时间,观测其运行状况一直比较稳定,经济效益显著。
采用APC技术可以在DCS系统常规控制技术的基础上,投入少量的资金及劳动力,就能产生较好的收益,使工艺参数尤其是分馏塔、稳定塔的操作条件控制更加稳定可靠,实现卡边操作,使产品质量和生产能力得到提高,因而产生较好的收益。
1先进控制系统概况。
1.1先进控制技术概述[1,2]
先进控制是通过安装于计算机上的特殊软件与DCS上的PID调节器配合应用,对装置进行综合调节,同时满足生产中多个控制要求的技术。因为外界运行环境不断变化,而且参数具有未知性、时变性、突变性以及不稳定性,复杂工业系统往往具有不可预测性,这时用来处理复杂工业系统采用常规PID控制效果不好,常规PID控制器很少考虑到变量之间的相互作用,而且是在被控参数产生偏差后才进行调节。由于装置变量之间总是存在相互作用,因此采用先进控制技术往往效果较好。先进控制器中包含有装置信息,根据来自系统外部的干扰信息和生产中的调节信息,先进控制器可以预测出装置未来的变化趋势。先进控制在满足了多个控制要求之后,能够根据操作人员设置的参数,进一步实现生产综合效益的最大化。
先进控制是一套工业应用软件,它将整个生产装置或者某个工艺单元作为一个整体研究对象,首先通过现场测试,量化描述各变量之间的相互关系,建立过程多变量控制器模型。利用该模型可以预测装置的变化,提前调节多个相关的操作变量,因而可提高装置运行的稳定性。通过实施先进控制,改善工业生产过程动态品质,减少关键变量的波动幅度,使其更接近于理想目标值,从而将工业生产过程推向更接近装置约束临界条件下运行,保证产品质量的稳定性,提高目标产品的产率及生产装置的生产处理能力,降低生产运行成本、减少装置能耗、提高经济效益,最大限度地满足动态多变市场的需求,提高目标产品的市场竞争力。
1.2先进控制技术的工作原理
多变量先进控制技术,是以过程计算机系统及其上位机为实施平台,以常规控制为基础,突破了常规PID控制的控制回路各自独立的工作模式,以整个生产装置或装置单元为对象,根据各变量间的模型关系,利用先进控制方法对装置实施协调统一的控制。
现阶段先进控制技术在石油化工生产装置的应用,普遍采用的是预测控制技术。预测控制技术,采用“模型预测、反馈校正、滚动优化”的控制算法,根据对将来几步的预测,决定走当前一步,参见图1。而常规PID控制,是基于误差的控制,即“走一步,看一步”。
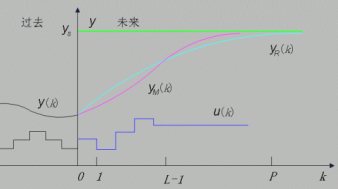
图1 预测控制基本原理示意图
由于先进控制把主要被控对象和控制量全部纳入控制系统,因而具有良好的跟踪性能。先进控制在偏差控制的基础上,将过程模型作为控制器内部模型,提高过程信息和知识利用率,可以实现多目标协调优化控制。[3-5]
1.3先进控制系统结构[6]
先进控制软件是美国AspenTech公司的DMCplus,控制系统如图2所示。基于不可测变量在线计算和常规PID控制系统的先进控制系统,上连优化,下接常规控制。其主要目的是取得比常规PID控制更好的控制性能,质量平稳卡边,在不超约束的条件下,使生产过程随时运行在优化状态,尤其对多变量互相关联的生产过程,PID控制常常无能为力,先进控制具有明显的优势。其主要特点:通过调整常规PID控制器的给定值,实现先进控制器的控制作用,即PID的给定被作为先进控制的操作变量。当先进控制投用后,作为先进控制调节手段的PID控制器的给定值由先进控制调整,不再由操作员调整。
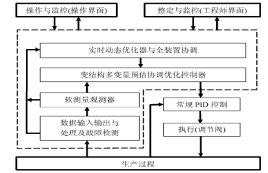
图2 先进控制系统结构
2、先进控制系统的实施
2.1 反再分馏先进控制器
催化裂化分馏塔的任务主要是把反应送来的油气混合物按沸点范围分割为富气、汽油、轻柴油和油浆等馏分,并保证各个馏分的质量符合规定的要求。
反再分馏先进控制器运行周期为1分钟,控制器见图3:

图3 反再分馏先控系统操作画面
分馏系统先进控制器主要有以下控制指标:
1)重要变量平稳控制。包括分馏塔顶温度、塔底温度、各侧线抽出温度以及回流罐液位和塔底液位的平稳控制。
2)质量卡边控制。通过利用基于过程动态数学模型的软测量技术,该系统可以实时给出分馏塔塔底液位、温度及各产品质量,将其控制在合格的范围内,并对粗汽油、轻柴油产品实现质量卡边控制。
3)多变量协调。在各种工况下,自动选择操作变量MV,使其被控变量CV达到控制要求,使操作变量及其相关变量不超限。
4)实时优化,节能降耗。在保证塔顶、塔底温度及产品质量合格的情况下,适当降低塔底换热器取热或塔顶回流量,实现节能降耗。
2.2吸收稳定先进控制器
吸收稳定单元的主要作用是加工来自分馏塔顶油气分离器的粗汽油和富气,分离出瓦斯和液化气,并产出合格的稳定汽油。由于涉及各塔、分离罐的串联操作,上游出料波动会对下游液位产生干扰,有时候会引起较大波动。设计吸收稳定先进控制器的主要目的是通过实施非线性液位以及液位速率控制,可以维持各塔、分离罐液位平稳,并在给定区域内,使上游出料波动减小,变化平缓,这样对后续单元操作以及转化率的计算都有益处。
吸收稳定系统先进控制器运行周期为1分钟,控制器见图4:
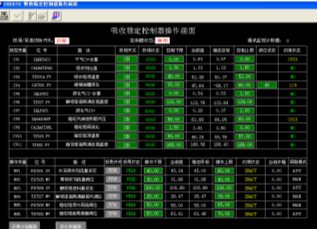
图4 吸收稳定先控系统操作画面
吸收稳定系统先进控制器主要有以下控制指标:
1)上下游协调控制。通过实施液位以及液位速率控制,可以维持各塔底、分离罐液位平稳,并在给定区域内,使进料流量变化平缓。
2)支路平衡以及液位非线性控制。吸收塔、解析塔和稳定塔都存在着支路平衡控制问题,同时还存在着液位控制问题。因此设计了一个大的非线性液位及支路平衡控制方案,在实现各支路温差控制的同时,实现了吸收稳定单元各塔液位的非线性控制。
3、先进控制器的投用
1、控制器的投用
1)检查,工况正常,仪表数据显示正常,各CV和MV的上、下限设置合理。
2)检查,计时器运行正常。
3)符合条件后,先检查各CV投入状态,如果不为“投用”,则修改其为“投
用”。检查各CV的投用状态是否都为”GOOD”,如果不是,依据操作画面使用说明中罗列的情况一一排除原因,解决不了的异常情况交由工程师处理。各约束状态是否都为”NORMAL”,如果不是,再次检查上、下限设置是否合理。
4)检查底层控制回路的控制模式是否处于投用APC要求的投用前(MAN或
者AUT),如果不是,修改为APC要求的投用前的控制模式AUT或MAN,两个先进控制器MV回路的投用前回路模式及投用后回路模式详见表1:
表1 先进控制器MV回路的投用前后回路模式
1)检查该MV仪表数据/当前值显示正常,上、下限设置合理 。
2)检查该MV的控制模型是否处于投用APC要求的控制前模式,如果不是,则需要将回路模式切换为自动AUT或者手动MAN模式。
3)将MV投用开关,切换到“投用”状态。
3、单个CV的投用
1)检查该CV仪表数据/当前值显示正常,上、下限设置合理。
2)启动该CV投用开关,等待MV的投用状态显示为”GOOD”, 则此时该变量进入先进控制监控,该变量投用过程结束。
4、单个DV的投用
DV的投用和切除操作由仪表工程师在上位机进行。
1)检查该DV仪表数据/当前值显示正常。
2)启动该DV投用开关,等待MV的投用状态显示为”GOOD”, 则此时该变量进入先进控制监控,该变量投用过程结束。
4、先进控制器的实施效果[7,8]
该系统自2012年5月投用,经过两年多的不断调整与完善,各项功能均达到了预期目的,先进控制系统已经初步发挥了作用,主要表现在以下几个方面:装置提高液收(汽油+柴油+液态烃)收率0.75%以上,这部分提高主要来自于焦炭、油浆等重组分产品产率的降低;系统自动化水平大大提高,降低了操作人员的劳动强度;系统运行安全平稳;改善了系统控制性能,主要控制指标平稳性提高;在平稳操作的基础上,对系统主要参数实行卡边控制,提高高价值产品收率,卡边控制带来了显著的经济效益。
I套催化裂化装置使用先进控制系统后,总体提高液收0.75%以上。液收是本装置重要产品,提高其收率意味着经济效益的提升,先进控制投用前后具体各产品收率变化情况如表2。
表2 先进控制投用前后各产品收率变化情况
此外,先进控制投用前后(2013年相比2012年1-4月)统计装置平稳率提高了0.2%,产品质量2012年1 -4月有24个点超厂控指标,而2013年仅有8个点超标,质量合格率提高了1.5%。由此可见,先进控制系统的应用显著地提高了各塔设备的操作平稳性,并实现了部分产品质量指标的卡边控制,改善产品质量,降低操作难度。与此同时,随着装置平稳性进一步的改善,使各塔设备的能耗大幅度地下降,实现装置的安全、高产、低耗、节能和减排。
5、结论
经过两年多的运行,先进控制系统运行可靠平稳,操作简便。实践证明先进控制技术在I套催化裂化装置上的应用效果是明显的,取得了显著的经济效益,为石油化工流程工业企业更好地实现“安稳长满优”提供更有力的支撑和保障,该先进控制系统是把高科技含量技术成果应用到实际生产装置上的一次成功应用。
参考文献:
[1]马伯文,催化裂化装置技术问答(第二版)[M].北京:中国石化出版社,2003.2.460-464
[2] 张 舟,林 伟.催化优化控制的应用[J].石油化工自动化,2004,(2):20-22
[3] Brosilow C. Inferenlial conrtol of process [J].AIChE. J.,1978,24(3):485-509
[4] 蔡飞云.利用PID在I/A's中实现常压炉四支炉温差控制[J].石油化工自动化,2003,(2): 11-13
[5] 王德康.基于OPC技术的先进控制软件设计与研究[J].化工自动化及仪表,2000,27(4):27-30
[6] 王强,刘勇,刘俊峰.先进控制与实时优化在催化裂化装置的应用[J].石油化工自动化,2006,(6): 23-27
[7] 王树青.先进控制技术及应用[M].北京:化学工业出版社,2001.99-108
[8] 王树青,金晓明.先进控制技术应用实例[M].北京:化学工业出版社,2005.202-222